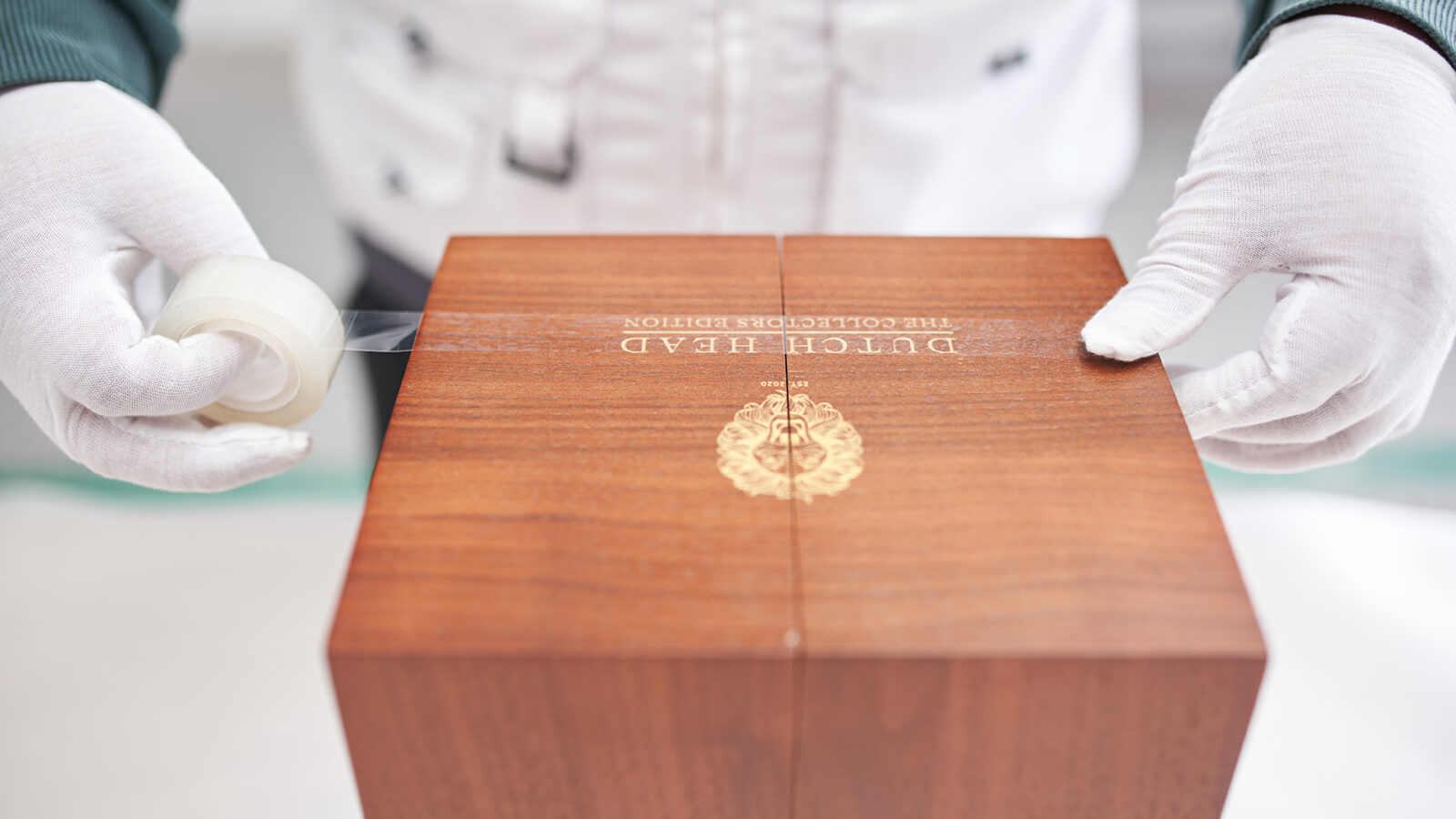
Pre-Shipment Inspection
A Pre-Shipment Inspection (PSI) is a final inspection before shipment. We assess the quality of products before they enter the container and are shipped.
A Factory Audit is an assessment of the working practices of suppliers abroad. This helps you as an importer to select the right supplier.
With a Factory Audit, we check the quality and reliability of a manufacturer. A professional auditor thoroughly inspects the factory and assesses whether the manufacturer can produce your desired product and deliver it on time.
Based on codes of conduct and quality standards, the auditor determines whether your potential new supplier meets the conditions you set. In doing so, he will identify at least the following:
You can extend the standard Factory Audit to include an audit of the following:
Facilities, and other business processes. With a Factory Audit, you detect these problems early so that worse is prevented. In this way, we support you as an importer in both transitioning to new suppliers and assessing existing business relationships.
We support you as an importer in both transitioning to new suppliers and assessing existing business relationships. There are different types of factory audits to assess suppliers’ business processes.
Assuming social responsibility is an indispensable part of the procurement process. Ethical audits assess working conditions in a factory and ensure that no human rights are violated. This is done based on SA8000 (Social Accountability 8000). Structural audits measures, and compliance with relevant codes and standards, among other things.
A production audit provides insight into the manufacturer’s capacity: can it make the product you want and deliver it on time? If so, you have an assurance that all product requirements are met.
To know whether a plant complies with local laws and regulations regarding environmental protection, we conduct environmental audits. Here, the auditor checks for compliance with the required environmental standards (based on ISO 14001), so that environmental management is constantly improving.
A quality audit shows whether the manufacturer has an effective quality management system (based on the ISO 9001 standard). This amounts to assessing whether the manufacturer can meet all requirements, including those set by you.
A Pre-Shipment Inspection (PSI) is a final inspection before shipment. We assess the quality of products before they enter the container and are shipped.
A First Article Inspection (FAI) clarifies whether the manufacturing process meets your desired specifications. As an importer, the inspection of the first article is important in assessing product quality.
An During Production Check (DPC) detects quality defects at an early stage. This gives you as importer enough time to take appropriate measures and the production line functions optimally.
With a Container Loading Check (CLC), we monitor the loading process. This ensures that your orders are not unnecessarily delayed and that they reach their destination damage-free.